Applicazione dei sensori ultrasonici CSB18 nel monitoraggio del diametro del rotolo
- Condividi
- editori
- Zoe
- Data Emissione
- 2024/9/13
sommario
Nelle moderne linee di produzione automatizzate, il monitoraggio in tempo reale del diametro del rotolo è fondamentale per garantire una produzione continua. Questa soluzione utilizza i sensori a ultrasuoni della serie CSB18 di DADISICK che, tramite prestazioni avanzate e sistemi di controllo intelligenti, monitorano in modo continuo e accurato il diametro di vari materiali, tra cui materiali trasparenti, lucidi, colorati, neri e metallizzati, automatizzando al contempo il processo di sostituzio
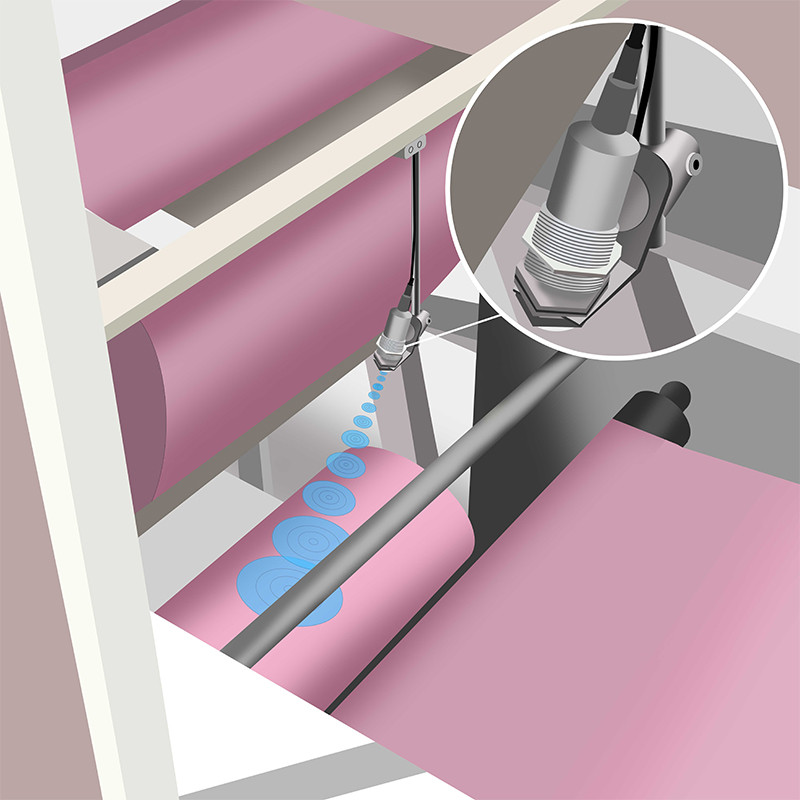
Applicazione dei sensori ultrasonici CSB18 nel monitoraggio del diametro del rotolo
Nelle moderne linee di produzione automatizzate, il monitoraggio preciso dei diametri dei rotoli non è solo un fattore critico per garantire una produzione continua, ma anche essenziale per mantenere un'elevata qualità del prodotto. Questa soluzione utilizza gli ultimi sensori a ultrasuoni della serie CSB18 di DADISICK che, attraverso prestazioni avanzate e sistemi di controllo intelligenti, possono monitorare in modo continuo e accurato il diametro di vari materiali (inclusi materiali trasparenti, lucidi, colorati, neri o metallizzati), automatizzando al contempo il processo di sostituzione dei rotoli. Ciò migliora significativamente l'efficienza della produzione e riduce i costi.
Nelle applicazioni pratiche, come mostrato nell'immagine sottostante, il sensore a ultrasuoni CSB18 misura il diametro del rotolo in tempo reale utilizzando la tecnologia senza contatto. Le linee d'onda blu nell'illustrazione rappresentano il modo in cui il sensore a ultrasuoni emette onde sonore e riceve segnali riflessi per misurare con precisione il diametro del rotolo. Questo metodo evita problemi come usura o contaminazione associati alla misurazione a contatto tradizionale, fornendo una soluzione di monitoraggio del diametro del rotolo altamente affidabile per linee di produzione automatizzate.
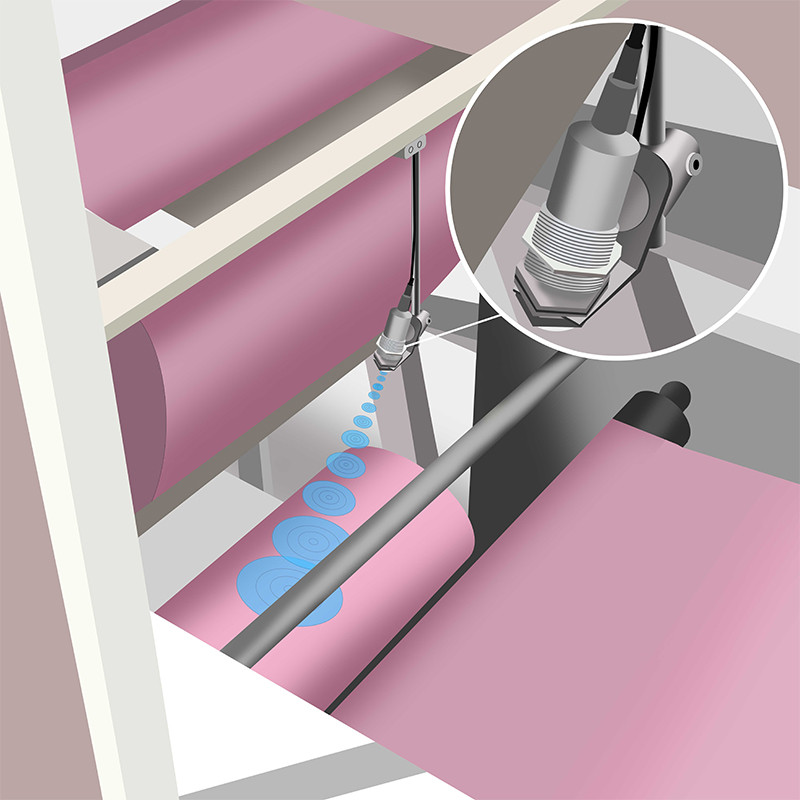
Componenti principali e caratteristiche tecniche
Misurazione senza contatto: utilizzando la tecnologia a ultrasuoni, il sensore effettua la misurazione senza contatto diretto con la superficie del rullo, evitando errori di misurazione causati da usura o contaminazione.
Ampia adattabilità: il sensore della serie CSB18 è in grado di penetrare materiali trasparenti, colorati e metallizzati e continua a funzionare stabilmente anche in ambienti estremi, il che lo rende adatto a settori quali l'imballaggio, la stampa e altri ancora.
Uscita analogica continua: fornisce segnali di corrente o tensione precisi che riflettono le variazioni del diametro del rotolo in tempo reale, consentendo ai controllori delle macchine di mantenere un controllo accurato.
Elevata affidabilità: gli algoritmi avanzati di elaborazione del segnale sopprimono efficacemente le interferenze ambientali, garantendo l'accuratezza e la stabilità dei dati di misurazione.
Modelli | CSB18-300 | Codice CSB18-500 | Codice CSB18-1000 |
Campo di rilevamento | 30-300 millimetri | 50-500 millimetri | 60-1000 millimetri |
Zona cieca | 0-30 millimetri | 0-50 millimetri | 0-60 millimetri |
Risoluzione | 0,1 millimetri | 0,15 millimetri | 0,17 millimetri |
Tempo di risposta | 22 millisecondi | 32 millisecondi | 52 millisecondi |
Isteresi di commutazione | 2 millimetri | 2 millimetri | 2 millimetri |
Frequenza di commutazione | Frequenza 45 Hz | Frequenza | Frequenza 19 Hz |
Ripetibilità: ±0,15% del valore di fondo scala | |||
Precisione assoluta: ±1% (compensazione della deriva della temperatura integrata) | |||
Tipo di input: Con funzione di sincronizzazione e apprendimento | |||
Tipo di uscita: Uscita di commutazione; Uscita IO-Link; Uscita analogica; Uscita digitale RS485 | |||
Materiale: placcatura in rame e nichel, raccordi in plastica, resina epossidica caricata con vetro | |||
Tipo di connessione: connettore M12 a 5 pin | |||
Classe di protezione: IP67 | |||
Temperatura ambiente: -25°C~+70°C (248~343K) |
Sistema di controllo intelligente
Acquisizione ed elaborazione dei dati: il sistema integra un efficiente modulo di acquisizione dati che elabora i segnali dei sensori in tempo reale, visualizzando i dati sul diametro della bobina in un formato numerico semplificato per un facile monitoraggio.
Meccanismi di avviso e allarme: il sistema è programmato con soglie di diametro superiore e inferiore. Quando il diametro della bobina scende al di sotto del valore preimpostato, attiva un segnale di avviso. Se continua a diminuire fino a un livello critico, il sistema emette un allarme di emergenza e avvia il processo di sostituzione della bobina.
Gestione automatizzata: tramite il collegamento con bracci robotici o sistemi di alimentazione automatica, il sistema consente la sostituzione automatica della bobina, riducendo al minimo l'intervento manuale e aumentando l'efficienza produttiva.
Monitoraggio e diagnostica da remoto: dotato di funzionalità di accesso remoto, il sistema consente alla direzione di visualizzare lo stato della produzione in tempo reale, eseguire diagnosi e apportare modifiche da remoto.
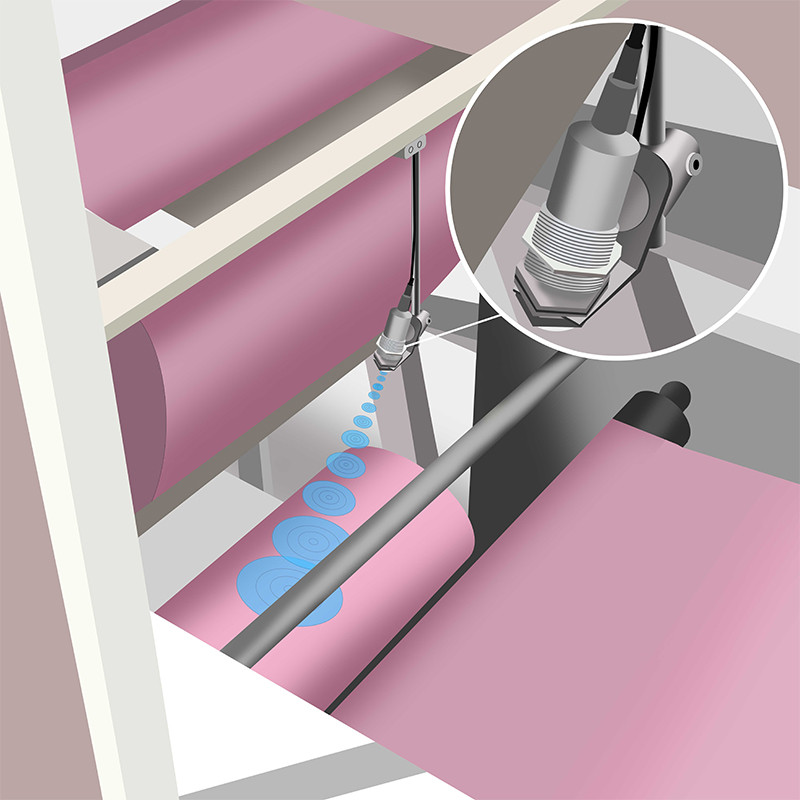
Fasi di implementazione:
1️⃣ Analisi dei requisiti: definire i requisiti specifici della linea di produzione, tra cui tipo di bobina, intervallo di diametro e frequenza di sostituzione.
2️⃣ Progettazione e selezione del sistema: scegliere sensori e sistemi di controllo appropriati in base ai requisiti e progettare l'architettura del sistema.
3️⃣ Installazione e messa in servizio: installare e mettere in servizio i sensori sulla linea di produzione, garantendo la precisione della misurazione e la stabilità del sistema.
4️⃣ Integrazione e test del sistema: integrare perfettamente il modulo di monitoraggio dei sensori con il sistema di controllo della linea di produzione ed eseguire test completi per garantire che tutti i moduli funzionali funzionino insieme in modo efficace.
5️⃣ Formazione e manutenzione: formare gli operatori sul funzionamento e la manutenzione del sistema e stabilire un piano di manutenzione regolare per garantire la stabilità del sistema a lungo termine.
Vantaggi del sistema
✅ Maggiore efficienza produttiva: il meccanismo automatico di monitoraggio e sostituzione delle bobine riduce i tempi di fermo, garantendo una produzione continua.
✅ Riduzione dei costi: riducendo al minimo l'uso eccessivo o la sostituzione prematura delle bobine, il sistema contribuisce a ridurre gli sprechi e abbassa i costi di manutenzione e manodopera.
✅ Miglioramento della qualità del prodotto: il sistema garantisce che le bobine vengano utilizzate in condizioni ottimali, prevenendo difetti di produzione causati da diametri insufficienti.
✅ Maggiore flessibilità: compatibile con bobine di vari materiali e dimensioni, soddisfa diversi requisiti di produzione.
✅ Facile integrazione e manutenzione: con un design modulare, il sistema può essere facilmente integrato nelle linee di produzione esistenti. Inoltre, offre comode interfacce di manutenzione e manuali operativi dettagliati per ridurre le difficoltà di manutenzione.
Sensori ad ultrasuoni correlati
Campo di rilevamento: 20-120 mm Campo di rilevamento: 20-200 mm Materiale: placcatura in rame nichelato Tipo di connessione: connettore M12 a 4 pin
Campo di rilevamento: 30-300 mm, 50-500 mm, 60-1000 mm Materiale: placcatura in rame nichelato, raccordi in plastica Tipo di connessione: connettore M12 a 5 pin
Campo di rilevamento: 100-2000 mm, 200-4000 mm, 350-6000 mm Materiale: placcatura in rame nichelato, raccordi in plastica Tipo di connessione: connettore M12 a 5 pin
Distanza tra emettitore e ricevitore: 20-40 mm, 20-60 mm, 20-100 mm Materiale: rame nichelato, raccordi in plastica Tipo di collegamento: cavo PVP da 2 m, 0,14 mm²